Related Pages:
Wire Frame Processing
Wire Frame Shipping
No losses occurred during shipping.
When the 50 blank frames were initially ordered they were delivered in two boxes of 25 frames. The frames were shipped in groups of two with a layer of bubble wrap between each frame in the pair and the cardboard protectors put on the outside of the pair. Packing peanuts were used around the frames to fill extra space in the boxes. This was reused multiple times for shipping and no frames were lost broken during shipping.
insert picture of box |
|
| insert picture of carboard | |
|
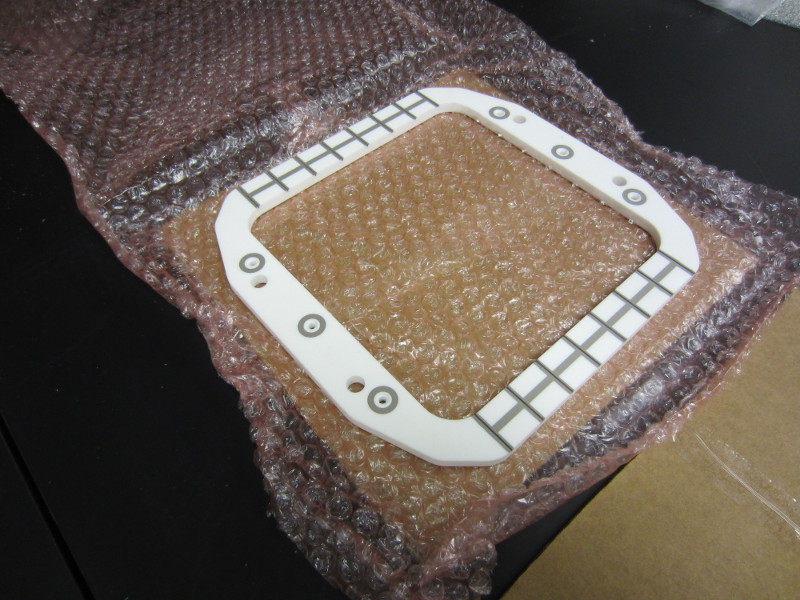
|
Wire Frame Manufacture
Frames were ordered as blanks with the inner and outer profile cut by the material supplier. This allowed some cost savings as the inside cutout was probably reused by the supplier.
Wire Frame Metallization
During the frame metalization a significant number of frames were lost during the firing stage. Roughly 4 HV frames and 6 signal frames were cracked during the firing process when the metallization was applied. There was also noticeable distortion when checking with a dial gauge on a flat table. Flatness was previously several thousandths of an inch deviation across the frame, and that increased to approximately of 0.020" at the largest deflections.
Wire Frame Soldering
During wire frame soldering some of the frames cracked during soldering. This resulted in the rev0 soldering procedure being replaced by the rev 1 solder procedure with shorter dwell times and lower solder tip temperature.
A wider shallower groove could have been useful to allow easier heating down into the groove as it was hard to get even a knife edge soldering tip to the lower part of the groove for tinning. Around 3 of the 50 frames also had significant metallization missing in the lower part of the groove and a message from the company that metalized the frames indicated it required special work to metallize the grooves rather than the usual screening process that were used for the other frame features. A shallow cup could have worked better than the narrow V that was used.
Wire Frame Cleaning
The metalization on the wire frames was removed by extended application of the ultrasonics, damage becoming visible after 15 or so minutes. As the flux remover and detergent baths both required ultrasonic cleaning it was decided to get with a 30 minute soak followed by 5 minutes of ultrasonics and that was found to give good results during the cleaning process, and keeping total time of ultrasonic cleaning at 10 minutes.
It was found about 15 frames could be done in each bath after which there was visible build up of material in the bath and it was changed.
The frame were cleaned in pairs and the frames were spaced off the bottom of the cleaner using the aluminum end plate for the frame stack and stainless steel ball bearings. The aluminum end plate was discolored by the detergent cleaner, and was later cleaned with an abrasive scrub pad to remove the coating.
It is generally recommended that items not be placed directly on the the bottom of the ultrasonic cleaner bath to prevent damage to cleaner and parts, but no problems were seen with the frames.
Frame Stack Assembly
UHV Safe Printed Circuit Boards
As component out gassing is required to be minimized during the experiment to maintain good operations standard PCB materials were not allowed to be used. This resulted in the use of a Rogers Duroid 6010 PTFE laminate for the PCB material. This cost about $1000 dollars per 12"x18" sheet, which was more than anticipated.
PCB fabrication almost always use Gerber files. This means that dwg, ipt, or others have to be redrawn before they can be used. This takes a professional about 8 hours at $80 an hour for a simple board with one trace and 8 holes to make the drawing and fab files. dwg to Gerber conversion programs exist and cost about $1500 but that can be useful if more than a few boards are required. Conversion is not fully automated and if a more than single layered board is required could require an extended amount of time.
A PCB layout programs such as KiCAD, which is free and open source, could be used. Advanced Circuits (website: 4pcb.com) has PCBArtist their own proprietary program that can send files only to them but seems to have a shorter learning curve is another option.
Once a board layout has been made a fabrication company in general wants to do one layout per sheet of material, and if two or more boards could fit on one sheet there are additional costs to make that setup. PCB fabrication also requires large spacing between boards on a sheet on order of 1" - 1.5" in most cases.
Thru holes in boards are 0.025" for 0.020" wire. It fits but it is hard to get the wires into the hole and through the board. 0.028" or 0.030" would probably have been better.
For the outer wires on the signal board should have gotten a solder patch to solder part of the wire to that would line it up with the holes in the PCB without letting it move around as much as it does a groove would have been ideal but a solder patch would have made things simpler.
Assembling Frame Stack
The initial frame stack assembly went well. The stack is fairly straight with only a small amount of variation (under 1/16") as the stack goes upward, and does not seem to have deviated to one side or another.
While cutting the wires off on the HV it was hard to clip the wires below the edge of the frame. The plan to leave the last millimeter or two unsoldered on the HV frames was only partially successful while making it easier to twist up the end of the wire for clipping and then pushing it back into the groove sometimes solder would flow or be placed to the end of the wire making this harder. A better solution would have been to stop the solder mask before the edge of the part so the solder would not flow as far and to make a little cone or step at the top to have space for the wire clippers to access the wire would have been better
Probably should have undersized the signal frame 20-30 thousands of an inch compared to the HV frames on the outside perimeter and oversized the through holes. This would have reduced the chance of leakage current from contact along the outside. Should not be an issue.
If the grooves in the 3 point mount comes could have been put to either top, bottom, left, or right instead of symmetrical around the center of the frame that would have allowed the wire frame orientation to be determined during assembly.
Soldering PCB Boards to Frame Stack
Ground boards went on fairly well as the longer wires made for more flexibility.
Signal boards were very stiff going on as the many short wires did not have a lot of flex. Breaking the board into two or three pieces with standoffs on some corners to stop sagging probably would have been a good idea to ease installation and to improve wire alignment.
HV boards had some problems in that the holes up from the bottom were offset from the board at some ends due to requirements to move around the mounting hardware for the other parts. This resulted in some potentially exposed wires as the wire had to be angled and beads don't cover as well in these cases.
Signal Readout
Groups of 8 signal wires from each plane would have been better, ADCs are almost always have channels in multiples of 8.
Two Dsub on one flange to one circuit board is an incredible pain to work around. Location tolerance is very high resulting difficulty to build and make fit. Two separate boards is recommended.
The ribbon cables can through longer than anticipated, and could have been shortened b 1-2 inches and still been able to attached easily to the feed thrus. This would have significantly complicated sliding the frame stack into the housing though.
If the plugs had been made symmetric that would have allowed the preamp boards to be rotated 180degrees. This would have been good for flexibility, but would possibly have allowed a reversed board to be used without noticing.
Putting Housing on Frame Stack
The housing was moved onto the frame stack by raising the jack beneath the frame stack upwards while the chamber remained stationary. This process went decently well but had some issues. The jack was a few inches short of what was required to close the chamber so near the end the jack had to be lowered while a large reference book was placed between the jack and the chamber to make up the last of the distance.
Previously we have looked at using multiple jacks under the chamber housing to lower it downwards. In retrospect this could have worked better starting with two jacks on either side with spacers and then transferring to two other jacks at 90 degrees to the first at the table level when it was lower. Combined with a bubble level this would have allowed the jacks to be lowered evening keeping the chamber straight during the process. The single jack took on an increasing angle as it was raised that required an increasing number of shims under one side of the housing to bring it back into alignment everytime it got too bad.
Clearances of 3/16" should have been the minimum instead of ~0.1". This lead to a few points where it was hard to clear the interior welds in the chamber especially with the chamber to housing angle that occurred. No visible damage was done but the difficulties could have been avoided.
Drain to ground boards should have been cut out around compression flange where they mounted and just put in place placed up by one bead. The higher spacing accomplished nothing and reduce clearances during assembly. The wires holding the board in place were more than sufficient for the task at hand and the board did not need the bolts at the top.
Survey and Alignment Measurements
A steady table is required. If the table is one wheels it will not work very well. Ours ended up being put up on jacks to stabilize the table during measurements.
For the twist that was found in the frame stack if survey and alignment had been called in before the boards were attached or wires fully clipped it would have been simple to try flipping alternate frames to remove the twist, but after soldering it was not possible.
For measure wire plane sag when horizontal a scribe mark along the side of the wire frames would have been easier to site along than the wires that refracted the light and were hard to see.
Gas Fill and Testing
During HV testing sparking occurred and the insulation on the HV input line had to be revisited. It looks like the chamber will be very hard to service in the event that anything goes wrong during operation. Frames stack can only be removed by undoing all sections, and the mount flange cannot be removed from its window without removing the whole housing. This will make any changes that may be requires somewhere between hard and impossible to make.
Experiences After Assembly
It looks like it will be nearly impossibly to do any changes to the chamber after assembly. The PCBs cannot be removed and it is a trial to remove the chamber from the housing.
There is some sparking inside the chamber that is severely limited the high voltage that can be applied to the chamber even after training it in. Part of the problem is the feed thrus in the He atmosphere can arc to their own ground, and part of the problem is the small clearances in the chamber.
Should have put 4-8 threaded holes in the compression plate to mount possibly future items. The current lack is making some possible chambers much hard to work.